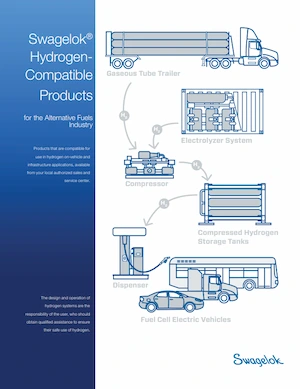
Download FREE
Swagelok Hydrogen-Compatible Products
for the Alternative Fuels Industry
This 33-page PDF shows Swagelok fluid system products compatible with hydrogen on‑vehicle and infrastructure applications. If you specify systems such as gaseous tube trailers, electrolyzer systems, compressors, dispensers, fuel cell electric vehicles, compressed hydrogen, and storage tanks, this PDF will be useful.
Instant Download
[PDC Machines manufacturers specialty hydrogen compressors for a variety of emerging hydrogen mobility applications.] Swagelok is the only brand and partner that we use throughout for tube fitting systems. It's not a supplier-vendor customer relationship; we view them as a partner for everything. We use them for our tube fittings we use them for our valves, instrumentation, fittings… we use it all over all of the products that we make.

Kareem Azfal, CEO, PDC Machines
in "Building Mission-Critical Hydrogen Compressors" video
Examples of considerations in hydrogen applications
Edmonton Valve & Fitting offers a wide range of hydrogen-compatible Swagelok components with top-quality metallurgy, leak-tight designs, and high-pressure resistance. We also offer EC-79-certified components suitable for on-vehicle applications, heavy-duty, rail, ship, and aerospace.
Leakage
- Pressure relief valves: Failure can occur during reseating or if the valve fails to maintain the seal pressure near the set pressure.
- Flanges: In addition to size and pressure classes, the sealing face must fully interface with the tubing adapter for different face styles such as flat, raised, RTJ, and tongue-and-groove. 316/316L stainless steel material further inhibits fugitive emission release.
- Welding: Connectors can be welded, provided the connection is not necessary for safety, maintenance, or modular design. An orbital weld system could be an option for repeatable, high-quality welds.
- Sampling systems: A closed loop sampling system can return purged fluid to the inlet.
Materials
- ASME B31.12 Standard on Hydrogen Piping and Pipelines provides material selection requirements and recommendations for hydrogen service. Austenitic stainless steels like 304 and 316 are recommended for all components in hydrogen service, and they should be used in the annealed condition if possible.
- Some carbon steels can be used for gaseous hydrogen service if operating temperatures are at least -29°C. Still, they are not recommended for high-pressure applications, as they are more susceptible to embrittlement than stainless steel.
- Aluminum alloys, copper, and copper alloys are also generally suitable for hydrogen service. However, nickel and nickel alloys are susceptible to severe hydrogen embrittlement and should never be used with hydrogen.
Steel
- With an atomic radius of just 53 pm, hydrogen is difficult to contain. Its small size and general reactivity to many common metals also lead to embrittlement. Under high pressures, hydrogen’s solubility into the surrounding metal increases, which provides a vector for material creep and crack propagation.
- High-nickel concentration 300-series (iron-nickel-chromium alloys) stainless steels are able to introduce austenitic structures into the workpiece below the critical eutectoid temperature of mild steel; 316/316L austenitic steel possess excellent qualities for resistance to hydrogen embrittlement.
Valves
- An important designation for any valve in a hydrogen plant is API 641 certification. The certification is granted to any quarter-turn valve that is able to withstand a battery of tests while maintaining a rate of emission less than 100 ppm.
Fittings
- Swagelok FK-series fittings are some of the only tube fittings engineered for the unique demands of hydrogen applications, with 316 stainless steel fabrication and pressure ratings up to 22,500 psi.
- In addition, SWS weld system are another valuable tool for hydrogen gas service in Alberta. These fixtures allow the welding of a gas-sealing connection that is an effective solution for hydrogen sealing.
Tubing
- Heavier tubing walls for hydrogen processes
Surface defects in tubing provide a likely path for escape; notably, the larger the outer diameter of the tube is, the greater the chance of sealing failures. To counteract the potential for leakage at seal points, heavier walls are recommended for tubing in hydrogen processes.